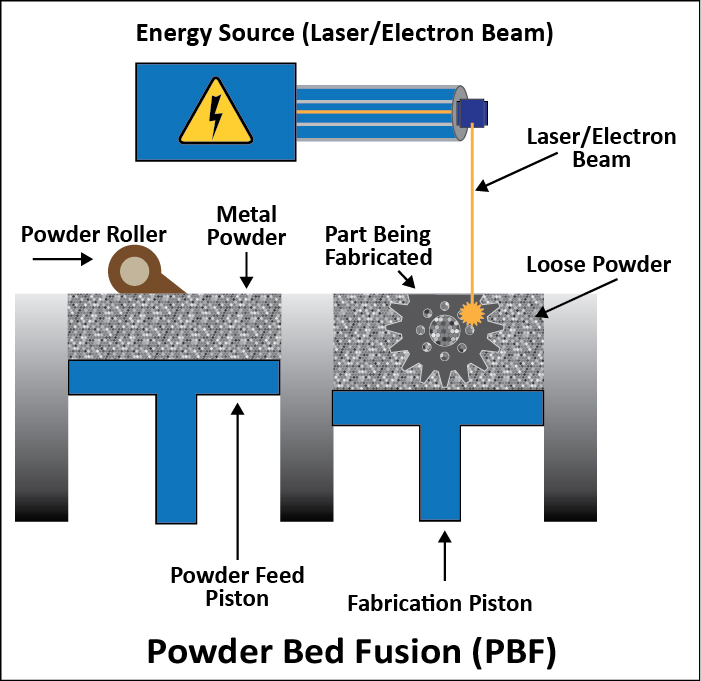
Powder Bed Fusion (PBF is a metal additive manufacturing process designed to use a high power-density laser to melt and fuse metal powders together.
PBF uses a variety of elemental or alloyed powders. Since the components are built layer by layer, it is possible to design geometries, internal features and challenging passages that could not be cast or otherwise machined. PBF produces strong, durable metal parts that work well as both end-use production parts and functional prototypes.
The process starts by slicing the 3D CAD file data into layers, usually from 20 to 100 micrometers thick, creating a 2D image of each layers. This file is then loaded into a file preparation software package that assigns parameters, values and physical supports that allow the file to be interpreted and built by different types of additive manufacturing machines.
With PDB, thin layers of metal powder are evenly distributed using a coating mechanism onto a substrate plate, usually metal, that is fastened to an indexing table that moves in the vertical (Z) axis. This takes place inside a chamber containing a tightly controlled atmosphere of inert gas, either argon or nitrogen at oxygen levels below 500 parts per million. Once each layer has been distributed, each 2D slice of the part geometry is fused by selectively melting the powder. This is accomplished with a high-power laser beam. The laser beam is directed in the X and Y directions. The laser energy is intense enough to permit melting (welding) of the particles to form solid metal. The process is repeated layer after layer until the part is complete.
Advantages of powder bed fusion (From https://engineeringproductdesign.com/knowledge-base/powder-bed-fusion/)
- Low cost – Comparatively low cost. Manufacturing cost has come down in the recent past due to the price drop in powder bed fusion machines cost.
- No or minimum support – Mostly these do not need the use of support structures as the powder acts as an integrated support structure. But to get more accuracy sometimes the bottom build plate is used as the support.
- Wide material choice – A large range of materials including ceramics, glass, plastics, metals and alloys can be used to make 3D objects
- Powder recycling – Powder could be recycled in some cases although to getter better parts some time there is a need to preheat the powder which might make the powder stick together
Disadvantages of powder bed fusion
- Relatively slow and long print time – Powder preheating, vacuum generation, cooling off period all adds to the build time making it one of the slowest in the additive manufacturing
- Post-processing – Printed parts need.. to be post-processed before usage adding time and cost
- Weak structural properties – Structural properties of these aren’t good compared to other manufacturing processes due to the layer based manufacturing.
- Surface texture – Since the parts are made fusing metal powder together, surface quality depends on the grain size of the powder and would be very similar to manufacturing processes like sand casting, die casting etc
- Support build plate – Although technically it does not need supports, to avoid any issues such as warping due to residual stress support may have to be provided. Also, most of the printers use a build plate to build the parts .. hence needs post removal and post-processing. This can be reduced by designing with that in mind.
- Powder recycling – The powder is expensive but even more expensive is throwing out residual partially melted or unused powder. To speed up the print process, the powder is often preheated. This means that some powder is affected by the heat despite not being in the final part.
- Thermal distortion – Another problem, mainly for polymer parts, is thermal distortion. This can cause shrinking and warping of fabricated parts.
- High power usage – Uses a lot of energy to create parts